Нержавеючая сталь - гэта металічны матэрыял, які ў машыне адносна складана. Існуе дзве асноўныя праблемы ў перапрацоўцы апрацоўкі: без беспадстаўнай сталі мае высокую высокую тэмпературу і моцную тэндэнцыю ўзмацнення працы, што лёгка насіць і паменшыць тэрмін службы інструментаў. ②stainless сталь мае вялікую трываласць, чыпсы не проста разбіць і лёгка пашкодзіць. Якасць апрацаванай паверхні таксама ўяўляе пагрозу для бяспекі аператара. Такім чынам, разрыў чыпа падчас павароту таксама з'яўляецца больш прыкметнай праблемай. У доўгатэрміновай вытворчай практыцы павароту дэталяў з нержавеючай сталі быў вывучаны інструмент знешняга павароту з нержавеючай сталі
Розная цвёрдасць мартенситнай нержавеючай сталі пасля цеплавой апрацоўкі аказвае вялікі ўплыў на перапрацоўку. У табліцы 1 паказана паваротная сітуацыя з сталі 3CR13 з рознай цвёрдасцю пасля цеплавой апрацоўкі з дапамогай паваротнага інструмента, вырабленага з матэрыялу YW2. Ві Гэта таму, што матэрыял мае вялікую пластычнасць і трываласць, няроўную структуру, моцную адгезію, і яго лёгка вырабляць рэжучы краю падчас працэсу рэзкі, і атрымаць добрую якасць паверхні. . Пасля тушэння і загартоўвання матэрыял 3CR13 з цвёрдасцю ніжэй HRC30 мае больш якасную працу і лёгка дасягнуць лепшай якасці паверхні. Хоць якасць паверхні дэталяў, апрацаваных, калі цвёрдасць перавышае HRC30, інструмент лёгка насіць. Такім чынам, пасля таго, як матэрыял трапляе ў фабрыку, спачатку ажыццяўляецца працэс тушэння і загартоўкі, а цвёрдасць дасягае HRC25-30, а потым праводзіцца працэс рэзкі.
Выбар матэрыялаў інструментаў
Прадукцыйнасць рэзкі матэрыялу інструментаў звязана з трываласцю і прадукцыйнасцю інструмента, а выраб матэрыялу інструментаў уплывае на выраб і якасць завострання самога інструмента. Такім чынам, матэрыял інструментаў павінен быць выбраны ў якасці матэрыялу інструментаў з высокай цвёрдасцю, добрым адгезійным супрацівам і трываласцю. Пад тымі ж параметрамі рэзкі аўтар правёў тэст на параўнанне на інструментах некалькіх матэрыялаў. З табліцы 2 відаць, што знешні інструмент для павароту з Tic-Ticn-Tin Composite Lide мае высокую трываласць і высокую якасць паверхні нарыхтоўкі. Добрая, высокая прадукцыйнасць. Гэта таму, што лопасці такога кшталту карбіднага матэрыялу маюць лепшую трываласць і трываласць, і таму, што паверхня мае больш высокую цвёрдасць і зносаўстойлівасць, меншы каэфіцыент трэння і больш высокую цеплавую ўстойлівасць, і яна стала добрым інструментам для ўключэння нержавеючай сталі ўключэння Такары з ЧПУ і першы выбар для знешніх інструментаў павароту для апрацоўкі 3CR13 з нержавеючай сталі. Паколькі не існуе рэзкі ляза гэтага матэрыялу, тэст параўнання ў табліцы 2 паказвае, што выніковая прадукцыйнасць замацаванага карбіду YW2 таксама добра, таму лязо матэрыялу YW2 можа быць выкарыстана ў якасці рэзкі.
Выбар геаметрычнага кута і структуры інструмента
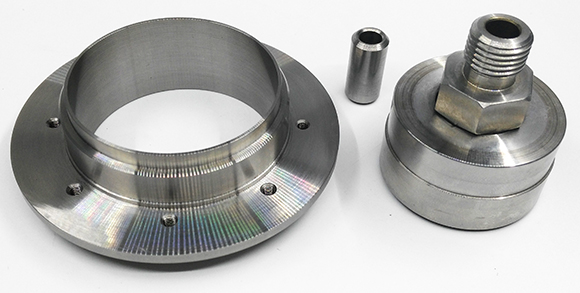
Для добрага матэрыялу інструментаў асабліва важна выбраць разумны геаметрычны кут. Пры апрацоўцы нержавеючай сталі геаметрыя рэжучай часткі інструмента звычайна варта ўлічваць з выбару кута грабля і кута спіны. Пры выбары кута граблі, варта ўлічваць такія фактары, як профіль флейты, наяўнасць або адсутнасць фашынг і станоўчы і адмоўны кут нахілу ляза. Незалежна ад інструмента, пры апрацоўцы нержавеючай сталі неабходна выкарыстоўваць большы кут граблі. Павелічэнне кута грабля інструмента можа паменшыць супраціў, які ўзнікае падчас рэзкі і выдалення чыпаў. Выбар кута афармлення не вельмі строгі, але ён не павінен быць занадта малым. Калі кут афармлення занадта невялікі, гэта выкліча сур'ёзнае трэнне з паверхняй нарыхтоўкі, пагаршаючы шурпатасць апрацаванай паверхні і паскараючы знос інструмента. І з -за моцнага трэння ўзмацняецца ўплыў загартоўкі працы на паверхні нержавеючай сталі. Кут дапамогі інструмента не павінен быць занадта вялікім. Калі кут рэльефу занадта вялікі, кут кліну памяншаецца, трываласць пярэдняга краю памяншаецца, а знос інструмента паскараецца. Звычайна кут рэльефу павінен быць належным чынам большым, чым пры апрацоўцы звычайнай вугляроднай сталі. Звычайна пры павароце марленічнай нержавеючай сталі, кут грабля G0 інструмента пажадана 10 ° -20 °. Кут рэльефу A0 падыходзіць для 5 ° ~ 8 °, а максімум не больш за 10 °.
Акрамя таго, кут нахілу ляза LS, адмоўны кут нахілу ляза можа абараніць кончык і палепшыць трываласць ляза. Звычайна G0 выбіраецца ад -10 ° да 30 °. Кут уводу KR павінен быць выбраны ў адпаведнасці з формай нарыхтоўкі, месцам апрацоўкі і ўстаноўкай інструмента. Шырокасць паверхні рэжучага краю павінна быць RA0,4 ~ 0,2 мкм.
З пункту гледжання структуры інструментаў, для знешніх інструментаў павароту выкарыстоўваюцца вонкава нахільныя кругавыя выключальнікі дугі. Радыус керлінгу чыпа на кончыку інструмента вялікі, а радыус кёрвання чыпа на вонкавым краі невялікі. Чыпсы паварочваюцца на паверхню, каб быць апрацаваны і разбіты, а разрыў чыпа добра. . Для рэжучага інструмента, кут другаснага адхілення можа кантраляваць на працягу 1 °, што можа палепшыць умовы выдалення чыпа і пашырыць тэрмін службы інструмента.
Разумны выбар сумы рэзкі
Колькасць рэзкі аказвае большы ўплыў на якасць паверхні нарыхтоўкі, даўгавечнасць інструмента і прадукцыйнасць апрацоўкі. Тэорыя рэзкі мяркуе, што хуткасць рэзкі V аказвае найбольшы ўплыў на тэмпературу рэзкі і трываласць інструмента, затым і надыходзіць Feed F і AP найменшы. Глыбіня разрэзу АП вызначаецца памерам нарыхтоўкі на паверхні, апрацаванай інструментам на такарным становішчы. Вызначаецца памерам матэрыялу пустым, звычайна 0 ~ 3 мм. Хуткасць рэзкі складаных і машынных матэрыялаў часта значна ніжэй, чым у звычайнай сталі, паколькі павелічэнне хуткасці прывядзе да моцнага зносу інструмента, а розныя матэрыялы з нержавеючай сталі маюць свае розныя аптымальныя хуткасці рэзкі. Гэтая аптымальная хуткасць рэзкі толькі гэта можа быць вызначана эксперыментам альбо кансультацый з адпаведнай інфармацыяй. Пры апрацоўцы з замацаванымі інструментамі карбіду звычайна рэкамендуецца хуткасць рэзкі v = 60 ~ 80 м/мін.
Хуткасць падачы F аказвае меншы ўплыў на трываласць інструмента, чым хуткасць рэзкі, але гэта паўплывае на разрыў чыпа і выдаленне чыпаў, што ўплывае на дэфармацыю і ізаляцыю паверхні нарыхтоўкі і ўплывае на якасць апрацоўкі паверхні. Калі шурпатасць апрацаванай паверхні не высокая, F павінна быць 0,1 ~ 0,2 мм/г.
Карацей кажучы, для складаных і машынных матэрыялаў звычайна выкарыстоўваецца меншая хуткасць рэзкі і сярэдняя колькасць падачы.
Выберыце правільнае астуджэнне і змазную вадкасць
Астуджальная змазка, якая выкарыстоўваецца для павароту з нержавеючай сталі, павінна мець высокія характарыстыкі астуджэння, высокія характарыстыкі змазкі і добрую пранікальнасць.
Высокая прадукцыйнасць астуджэння гарантуе, што можа быць забрана вялікая колькасць рэзкі. Нержавеючая сталь мае высокую трываласць, і лёгка вырабляць забудаваны край падчас рэзкі і пагаршацца апрацаванай паверхні. Гэта патрабуе астуджальнай змазкі, каб мець больш высокія змазкі і лепшую пранікальнасць. Звычайна выкарыстоўваецца апрацоўка змазкі астуджэння з нержавеючай сталі ўключае сульфураванае алей, сульфурызаванае соевае алей, газа плюс олеінавай кіслаты або расліннага алею, чатырохзоркавы вугляродны алей, эмульсія, эмульсія і г.д.
Улічваючы, што сера аказвае пэўнае агрэсіўнае ўздзеянне на станка, агародніннае алей (напрыклад, соевы алей) лёгка прымацаваць да станка і стаць нясвежым і пагаршаецца. Аўтар абраў сумесь чатырохручнага вугляроду і маторнага алею ў вазе 1: 9. Сярод іх чатырохручны вуглярод мае добрую пранікальнасць і добрую змазку маторнага алею. Выпрабаванні даказалі, што гэтая астуджальная змазка падыходзіць для паўфуніравання і аздаблення працэсаў дэталяў з нержавеючай сталі з невялікімі патрабаваннямі шурпатасці паверхні і асабліва падыходзіць для перапрацоўкі дэталяў мартычнай нержавеючай сталі.